SUSTAINABILITY UPDATE
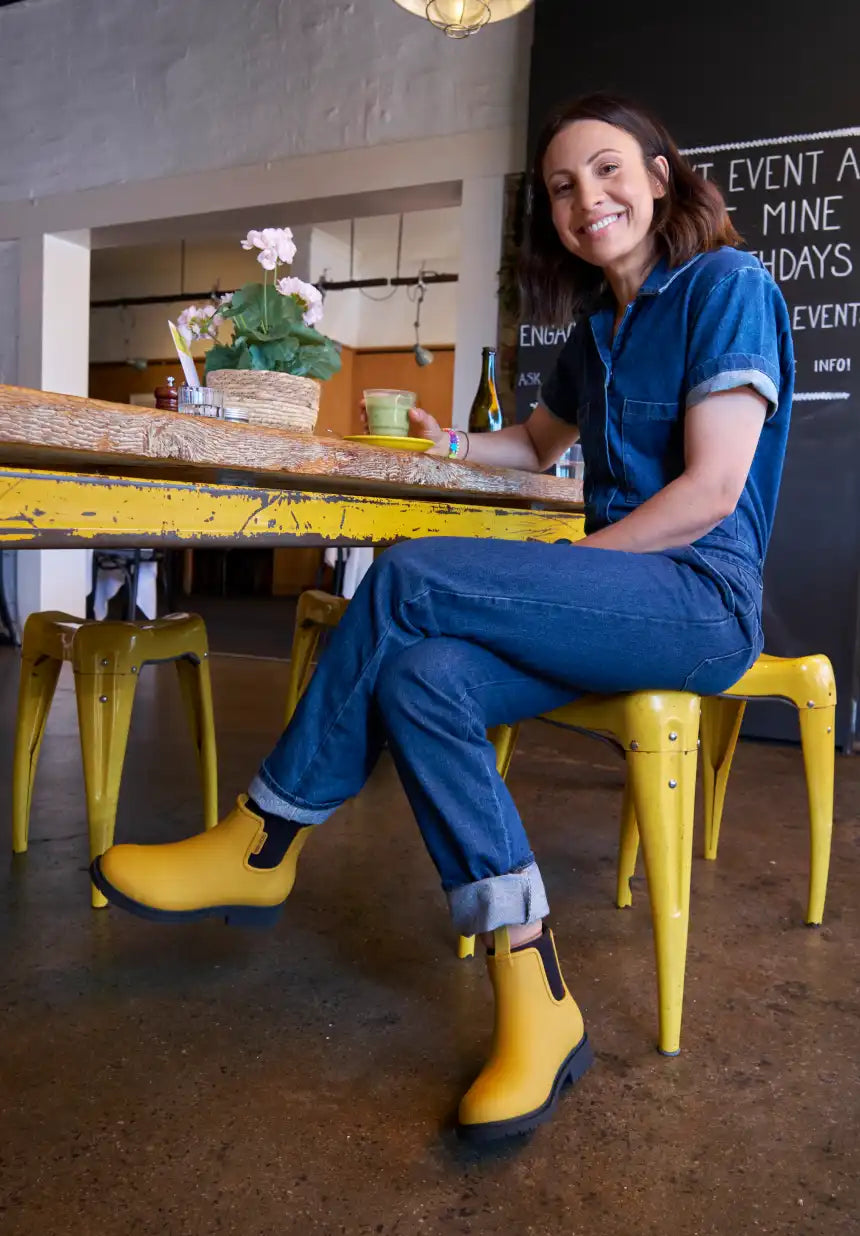
October 2024.
At Merry People our goal is to make the world a merrier place.
We are led by our brand values in how we do business and recognise the responsibility in what we bring into the world and how we operate.
Over the last 12 to 18 months, our focus has been on gaining full transparency regarding our supply chain and carbon footprint. We wanted to take steps to genuinely reduce the impact we are having on the world, and not by simply doing what was ‘trending’ in sustainability. As part of this process we needed to quantify our carbon emissions and understand what actions we could take to reduce them.
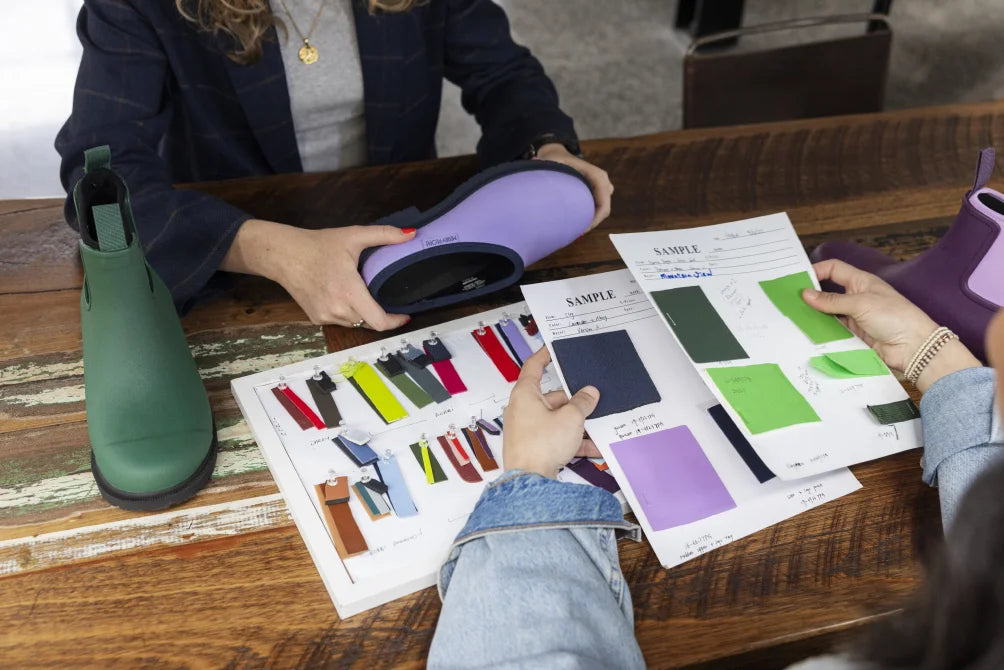
What Have We Done to Gain Understanding?
In 2024 we engaged an industry expert (Pangolin) to facilitate a full Life Cycle Analysis (LCA) of our Bobbi boot. It was recommended we only map the impacts of one product as a starting point - and we chose our Bobbi boot because it is the vast majority of our sales.
Our goal was to track the entire journey of the Bobbi boot from pre-production to end-of-life management to understand its impact.
We worked closely with our factories to gain a detailed understanding of all the processes involved in gathering and producing our raw materials, the production processes, including how the factory was managed; waste management, electricity sources & consumption. We tracked how our finished boots were sent to our warehouses around the world and from there to our customers. Then finally how our worn and unworn damaged boots were disposed of.
At every step, we needed data and documents to support the journey of the Bobbi boot. This data was provided to the team at Pangolin to validate and then calculate the carbon footprint of a Bobbi boot. It was an extensive task, but we are proud to truly understand what changes are needed to lower our carbon footprint, and to validate improvements we have already made. Beyond the knowledge of our carbon footprint, this process has given us a more transparent and traceable supply chain.

What Have We Learned?
Our Bobbi boot creates on average 11.6 kg CO2-e of emissions in its full life cycle. This is in line with general footwear, but gives us lots of room to improve. To put this into perspective, making 86 Bobbi boots causes the same emissions as flying from Adelaide to Melbourne in economy class five times, or sending 476 kg of food to landfill.
The materials that make up the Bobbi boot are the most significant driver of the carbon footprint, contributing 37.4% of total emissions. Rubber makes up most of Bobbi’s raw material followed by the neoprene lining (which is inclusive of SBR foam and two layers of polyester jersey).
The second largest contributor is the assembly stage, contributing 26.7%. This includes the power and resources used during manufacturing in our factories.
The third largest driver at 17% is the transportation of the Bobbi boots from our local warehouses to the customer. End of life makes up 8.4%.
What Have We Done to Improve?
MATERIALS
In July 2023 Merry People signed with Forest Stewardship Council (FSC) as a promotional license holder. FSC takes a holistic approach to using responsibly sourced pulp for our packaging and rubber for our boots from tightly audited and regulated plantations. FSC looks at not only the management of the world's forests, but also at how they are forested to ensure the workers are fairly paid and treated. You can read more about them here.
Natural rubber - We first started using FSC rubber in our newer styles, Tully and Fergie since launch and from July 2024 we will be using FSC-sourced rubber for the upper and outsole of our Bobbi boot and the upper of our Andie boot. We currently use virgin (new) natural rubber for Billie, Darcy, and Bobbi Kids styles however, we will be moving all styles to FSC in 2025.
Chemicals – we regularly run and pass tests on all of our major components to ensure we adhere to the REACH regulations of Restricted Substances and are not using chemicals that can be harmful. Our chemist is reviewing in detail all of our compounds and helping us to identify where we can switch to ingredients with less impact.
Neoprene - We use a virgin synthetic neoprene for the lining of our products, made up of SBR (Styrene-butadiene rubber) and two layers of Polyester jersey. We are currently testing the bio-based alternative for the foam with RPET polyester for the jersey and are looking to introduce this into new styles in 2025.
Insoles - Our Tully, Fergie and Andie boots use recycled PU (Polyurethane foam). We are testing other options of recycled or sustainable materials that will also offer a more comfortable wear experience, with the aim of updating the Bobbi insole in the next six months. We are currently using EVA (Ethylene-Vinyl Acetate) in our Bobbi, Billie, Darcy, and Bobbi Kids styles.
Packaging - all of our boots, socks and care kits are packaged in FSC Mix - 80% recycled fiber and 20% FSC-certified virgin (new) materials - to give the strength we need to protect the product and to be shipped safely. We don’t coat our papers so all of our packaging is fully recyclable.
We recently reduced our box sizes so that we could fit more pairs of boots into each shipping container, helping to reduce our carbon footprint for shipping. We use compostable bags for our hats and raincoats. We currently use a recycled plastic mailer however, we are now researching and testing how to eliminate all plastics in our packaging – watch this space as we work through the logistics.
MANUFACTURING
Our factories are regularly audited with leading auditing companies. These independent audits cover not only the environmental practices of the factory but the health and safety of workers, labour rights, pay, and ethical practices.
We also have our factories sign our own Code of Conduct that you can read here. This code ensures the staff who make our products are treated well and in line with workers' rights, fair pay and conditions according to local government regulations.
Water – we found via the LCA that our water usage was minimal and the water that is used is treated before going back into the system. It is also highly regulated and regularly tested by local government agencies.
Power - we have raised with our factories our desire for them to use renewable energy sources like solar. Each factory owner is receptive to the idea, however we appreciate that this will take time and lobbying of other factory clients. We will continue these conversations with our factories and will help inform new factories we work with.
Waste - nearly all of our rubber offcuts are recycled and remixed to make more rubber. The excess neoprene and jersey are sent by our factories to be recycled locally. For a deeper look into how our boots are made click here.
TRANSPORT
This is a big issue that the LCA shone a light on. We already had some understanding of the impact of airfreight /travel, but seeing in numbers how this has and will continue to contribute to our impact was insightful. We sea freight all of our boots to our warehouses located in Australia, England and Canada. Our operations team is reviewing ways to increase efficiency by minimising the distance our boots travel, preferably not by air, to our customers. Long term we need to look at getting products made closer to the selling market if it is commercially viable.
END OF LIFE
What to do with those boots that are returned or not quite right? In 2024, we donated approximately 500 boots to Thread Together who distributed them to those affected by the North Queensland floods. We continue to donate wearable but non-saleable products.
In Australia, unwearable samples and returns are sent to Save our Soles where they are recycled into flooring.
We are working through ways to facilitate the return and recycling of our boots once they no longer look their best.
To avoid excess stock holdings, we only order what we think we will sell and promote conscious shopping. We never go on sale to help prevent overconsumption.
QUALITY
The key to making a sustainable product is to give it the longest lifetime that we can. We keep this front of mind with all new products, designing and making our boots to perform over years of wear. We test all our styles whilst in the development phase and each production run rigorously with third party laboratories. We test for waterproofness, slip resistance, the strength of bond between outsole and upper, and abrasion resistance, amongst many others. We offer a 12-month warranty on all our products. Quality will always be a focus for us. We love hearing of stories of people who have had our product for all the years we have been in business!

Where to Next?
We are really excited to have gained this insight into our impact, however it is just the starting point for us!
We now have a pipeline of projects that we will continue to work through based on our findings and this information has now informed decision making on new products and new factory relationships.
We know we are not perfect, but we want to do the best we can to genuinely reduce our impact. We will continue to do LCAs on our Bobbi boots to track our progress and share with you our results.
Thank you for following our sustainability journey to date. We will provide another website update mid-2025.
Kindest,
Dani + the Merry People Team